Specification for aggregates for asphalt
AS 2758.5-2020 pdf download.Aggregates and rock for engIneerIng purposes Part 5 : Specification for aggregates for asphalt.
For the purpose of this document, the terms and definitions in AS 2758.0 apply.
4 Sampling
Sampling of an aggregate shall be carried out in accordance with the methods in AS 1141.3.1.
NOTE 1 The frequency of sampling should be nominated In the works specification or the supply agreement or as agreed with the supplier. In the absence of any of these documents, refer to AS 2758.0: 2020 Appendix A for a sampling scheme.
NOTE 2 Reference samples may be taken during the course of supply and retained for later testing.
5 Testing
Testing of aggregates shall be carried out in accordance with the relevant requirements of the applicable method.
Laboratories that perform the tests outlined in this document shall meet the requirements of AS
ISO/JEC 17025.
The testing requirements and specified limits for all asphalt aggregates are prescribed in Clauses 4 to 10.
NOTE A number of requirements in this document are fundamental and this specification provides a single test method and limits for these properties. Alternative test procedures and limits are presented for the determination of both shape and durability. For these properties, it is recommended that the test procedure and limits that are particular to the geographic area in which the aggregate source is located should be used in specifying supply.
6 Dimensional requirements
6.1 Particle size distribution requirements for aggregate
Particle size distribution test results in accordance with AS 1141.11.1, AS 1141.11.2 or AS 1141.12 (as appropriate) shall be provided to indicate the average grading of the aggregate proposed for supply. This shall be known as the nominated grading.
When required, a representative sample, the grading of which shall be the basis for acceptance of the quotation, tender or source of supply shall be provided. The grading of this sample shall be known as the nominated grading.
For each aggregate. the allowable tolerances for the supply of the nominated grading shall conform to the tolerances shown in Table 1.
6.2 PartIcle shape of coarse aggregate
The shape of aggregate particles shall be determined by one of the following methods:
(a) Particle shape — When determined in accordance with AS 1141.14, the proportion of misshapen particles in the fraction of coarse aggregate retained on the 9.5 mm test sieve, using a 3:1 ratio, shall not exceed 10 % and using a 2:1 ratio shall not exceed 35 %.
(b) Flakiness index — When determined in accordance with AS 1141.15, the flakiness index of coarse aggregate shall not exceed 35 %.
6.3 Crushed particles of coarse aggregate
When determined in accordance with AS 1141.18, coarse aggregate that is derived from gravels or conglomerates shall consist of at least 75 % by mass of particles with at least two crushed faces.
NOTE With the exclusion of quarries in hard conglomerates, coarse aggregates derived from a hard rock quarrying process where all particles are crushed do not require testing.
6.4 Shape of fine aggregate used in stone mastic asphalt
When determined in accordance with AASHTO T 304 Method A, the angularity of fine aggregate used in stone mastic asphalt shall be equal to or greater than 43 %. Stone mastic asphalt is defined as a gap graded wearing course mix with a high proportion of coarse aggregate that interlocks to form a skeletal structure which is bound with a mastic mortar.
7 Durability
7.1 General
Not more than one of the three sets of methods for the assessment of aggregate durability shall be specified. These sets of methods represent those most commonly used in Australia and are provided in this document. The set of methods specified should be the one which has been shown by local experience to be valid for rock sources likely to be used in the works.
NOTE All available tests and associated specification limits attempt to ensure adequate durability in service by measuring a change in properties over a short period of time (varying from minutes to days). This necessarily involves the imposition of conditions (e.g. loadings, temperature, exposure to reagents) that are unlikely to be met in service, in order to accelerate the change. Some aggregates may behave differently in service than predicted by a given durability testing regime. These differences arise from the different responses of the rock mineralogy and texture to the actual conditions. Experience with the material In service Is essential In Interpreting the testing results.AS 2758.5-2020 pdf download.
Specification for aggregates for asphalt
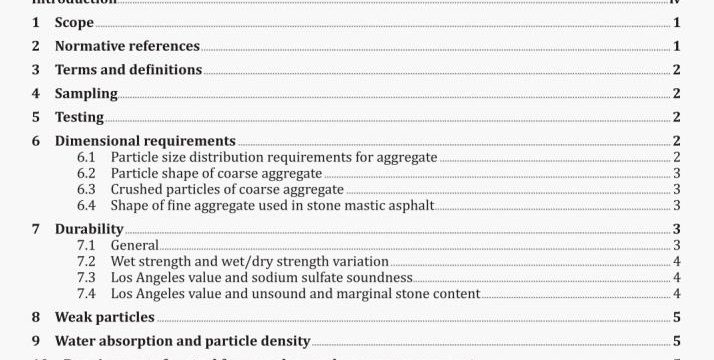