ASME B16-22:2012 pdf free download
ASME B16-22:2012 pdf free download.WROUGHT COPPER AND COPPER ALLOY SOLDER-JOINT PRESSURE FITTINGS
10.2 Threading Tolerances
Tapered pipe threads (NPT) shall be checked by use of plug or ring gages in either standard or limit types. When gaging internal taper threads, the plug gage shall be screwed hand-tight into the fitting. The reference pointforgaging internal productthreads depends onthe chamfer diameter. When the internal chamfer diameter exceeds the major diameter of the internal thread, the reference point shall be the last thread scratch on the chamfer cone. Otherwise, when the internal chamfer diameter does not exceed the major diameter of the internal thread, the reference point shall be the end of the fitting. In gaging external taper threads, the ring gage shall be screwed hand-tight on the external thread. On the external thread, the ring gage shall be flush with the end of the thread.
Tolerance for aninternalthreaded end havinganinter- nal shoulder shall be from the gage reference point (notch) to one turn small. Tolerance for an internally threaded end without a shoulder, and for an externally threaded end, shall be from one turn small to one turn large.
10.3 Design of Threaded Ends
The wrenching section of internally threaded ends shall be polygonal, and the wrenching section of exter- nally threaded ends shall be furnished with either poly- gon or flats, at the manufacturer’s option.
12.2 Optional Gaging
Method of Solder-Joint Ends For gaging the diameter tolerance of external and internal ends, the use of direct reading instruments instead of ring and plug gages as specified in para. 12.1 shall be permitted. When gaging the diameters of external and internal ends using direct reading instru- ments, refer to para. 9.3.
12.3 Standard Gaging
Method of Threaded Ends The standard method of gaging the externally and internally threaded ends shall be in accordance with the requirements of ASME B1.20.1.
NOTE: In gaging pipe threads, it is acceptable and common prac- tice to rap or tap the part to ensure proper seating of the gage. However, it is first necessary to clean both the gage and product threads to ensure that they are free of chips, burrs, abrasives, or other foreign materials.
ASME B16-22:2012 pdf free download
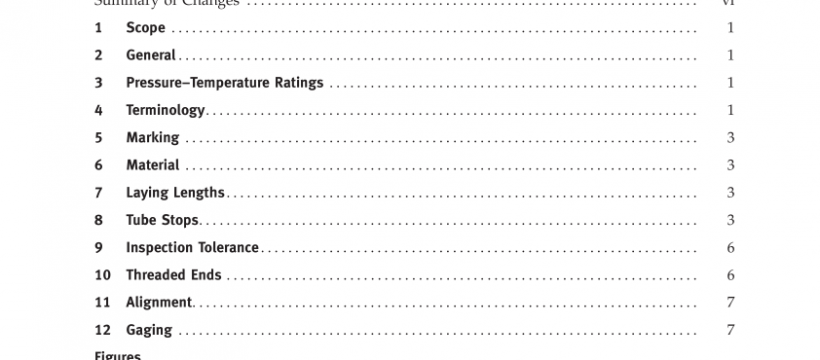